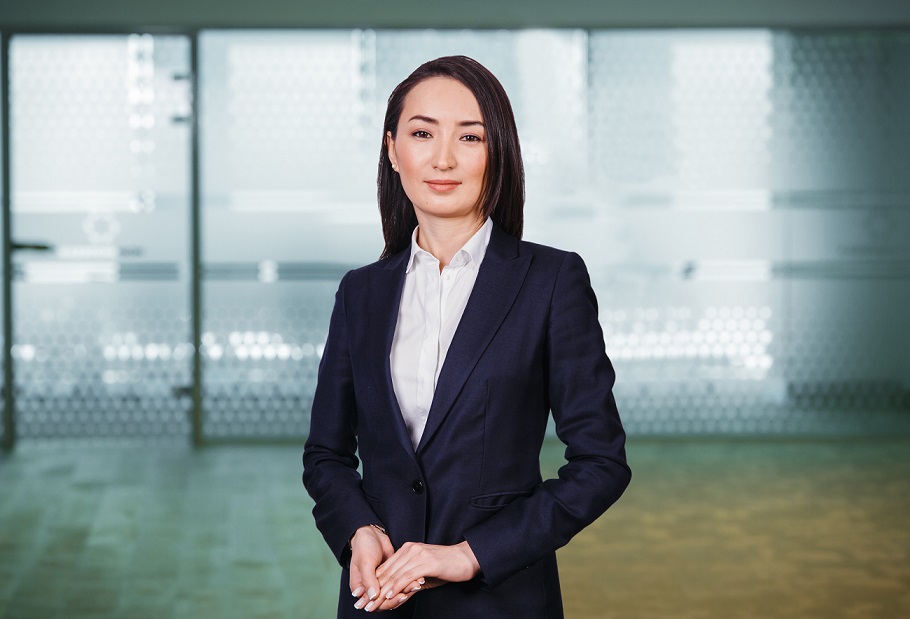
Проекты цифровой трансформации
Повышение эффективности производственных процессов и оптимизация затрат, применение лучших практик стали основой реализуемых проектов в АО «НАК «КАЗАТОМПРОМ». Об этом сегодня в интервью рассказывает и. о. главного директора по производству Алия Акжолова.
– Алия Хайдаровна, расскажите, пожалуйста, об основных направлениях производственной стратегии «Казатомпрома»? Какую роль в ее успешной реализации играет проектное управление?
– Сразу отмечу, что по поручению Президента Республики Казахстан заинтересованными министерствами в 2019–2020 годах проводилось форсайт-исследование развития и изменения приоритетов горно-металлургического комплекса Казахстана на 5–10 лет вперед. Результаты показали, что одним из элементов изменения приоритетов в ГМК на ближайшие годы является Recycling. В ходе проведения анализа затрат на производственные активы, техническое обслуживание и ремонт производственным департаментом «Казатомпрома» был выявлен потенциал для развития направления «Рециклинг оборудования и материалов при горно-подготовительных работах». Однако для совершенствования данного подхода требовались время и ресурсы, так как отсутствовала информация о процессах и исторических данных. После проведения соответствующего анализа в начале 2020 года принято решение о необходимости реализации данного направления посредством проектного управления. В марте прошлого года Совет по модернизации и трансформации «Казатомпрома» одобрил данное мероприятие и включил его в портфель проектов цифровой трансформации.
Если сказать вкратце, то при обустройстве новых блоков добычные предприятия закупают различные материалы и оборудование, которые после истощения ресурсов данных блоков остаются пригодными для дальнейшего применения в работе, однако не используются.
В ходе реализации проекта предприятия анализируют материалы и оборудование на предмет целостности, затем демонтируют и повторно используют на новых блоках, тем самым не расходуя бюджетные средства на закуп этих материалов и оборудования.
С учетом концепции по переходу к «зеленой» экономике были усовершенствованы текущие процессы, проведена полная инвентаризация всех материалов и оборудования, рассмотрены законодательные и корпоративные нормы, регулирующие данное направление на предмет его соответствия/несоответствия. Кроме того, разработан унифицированный регламент, включающий такие процессы, как поиск, оформление, утверждение, реализация, контроль и подтверждение выгод, расширены требования по безопасному монтажу и демонтажу оборудования и материалов в части соблюдения техники безопасности, охраны окружающей среды и радиационной безопасности. Немаловажно, что выстроен единый процесс при учете как технической, так и бухгалтерской документации, отражены ответственность работников, проанализирован коэффициент использования рециклинга и его дальнейшего увеличения без потери качества непрерывной производственной деятельности. Также внесены все необходимые изменения в проектные документы и проведен мониторинг имеющегося на предприятиях опыта рециклинга для дальнейшего тиражирования в другие ДЗО Компании.
И самое главное – разработан модуль для оцифровки всех бумажных данных в корпоративной информационной системе eKAP. Данная опция позволяет визуально отслеживать этапы реализации в диаграмме Ганта, вносить корректировки в режиме Agile и служит электронным хранилищем подтверждающих документов. Имея наглядно оцифрованные данные, можно активно управлять эффективностью данного мероприятия, что является одним из главных факторов успеха.
– Были ли сложности с проектом?
– Трудности представляло отсутствие информации, кейсов, лучших практик, которые можно было бы протестировать, поэтому производственный департамент полагался только на собственную аналитику и практику ДЗО. Безусловно, пандемия значительно изменила планы по реализации данного проекта, заставила критически пересмотреть свои взгляды на процесс. Работники производственного департамента каждый день проводили мозговые штурмы по реализации поставленных задач по принципу Think outside the box.
Необходимо отметить, что в выполнении производственной программы «Казатомпрома» на 2020 год мероприятия Recycling сыграли ключевую роль и наравне с другими проектами портфельных компаний АО «Самрук-Казына» признаны лучшими по итогам 2020 года.
Лидерами проекта являются предприятия «Инкай», ЮГХК, «Заречное», «Семизбай-U», при этом почти все добычные предприятия выполнили скорректированные в сторону увеличения планы работ за 2020 год.
Безусловно, решение
поставленных задач и достижение результатов были бы невозможны без
непосредственного вовлечения в проект руководителя мероприятия Ж. А. Садырбаева
и проектных менеджеров Шуриева Т. и Оразбека Н.,
которые контролировали работу в рамках проекта с предоставлением возможных
ресурсов для успешной реализации мероприятия, а также добычных предприятий «Казатомпрома».
Значительную помощь в координации данного мероприятия оказали и сотрудники
департамента цифровой трансформации.
Подтверждённые выгоды по
проекту по итогам 2020 года составили 1,814 млрд.
тенге
В 2021 году запланирован выход за рамки периметра добычных предприятий, план работ по расширению данного направления предоставлен в сервисные ДЗО «Казатомпрома», так как процесс рециклинга можно использовать на всех этапах производственной деятельности.
– Что еще вошло в портфель проектов и мероприятий цифровой трансформации АО «НАК «Казатомпром»?
– В рамках повышения производственной и операционной эффективности и снижения себестоимости были проведены мероприятия по переходу на использование водного раствора аммиака (25%) вместо каустической соды. Работы по организации применения в технологическом процессе переработки урана водного раствора аммиака (аммиачной воды 25%) вместо каустической соды были начаты в 2018 году по инициативе Горнорудного департамента. Данный химический реагент ежегодно возрастал в цене, а более дешевые альтернативные ему реагенты не всегда были доступны. В периметр мероприятий вошли 7 уранодобывающих предприятий – ТОО «Аппак», ТОО «СП «Хорасан-U», ТОО «ДП «Орталык», ТОО «Семизбай-U», ТОО «СП «ЮГХК», АО «СП «Заречное», ТОО «Каратау». Были проведены опытно-промышленные испытания, доказана техническая возможность и эффективность применения технологии, спроектированы и построены склады хранения аммиачной воды с линиями подачи реагента в технологический процесс.
Разумеется, реализация данных мероприятий не исключает возможности применения каустической соды, она будет закупаться в зависимости от лучшей цены на рынке. При этом перевод с одной технологии на другую не требует каких-либо финансовых или временных затрат.
В 2019 году мероприятие было включено в Портфель проектов и мероприятий цифровой трансформации АО «НАК «Казатомпром», а совокупный экономический эффект в части сокращения операционных производственных затрат от реализации мероприятия за 2019–2020 гг. составил 710 млн тенге. Капитальные затраты за этот же период составили 765 млн тенге. Ожидается, что данные затраты окупятся в течение 2021 года, а совокупный экономический эффект в части сокращения операционных производственных затрат от реализации мероприятия составит в этом году 831 млн тенге.
– Помимо экономического эффекта какое влияние оказывают мероприятия на безопасность труда работников?
– Внедрение технологии и организации линий подачи аммиачной воды благоприятно отразилось на уровне безопасности труда работников предприятий. Прежде всего исключена работа операторов по растворению сухой каустической соды, что снизило травмоопасность при погрузочно-разгрузочных работах и полностью исключило контакт с данным реагентом.
Стоит отметить, что линии подачи аммиачной воды могут быть полностью автоматизированы, и подача реагента в технологический процесс в необходимом количестве может происходить без непосредственного участия человека. Тем самым можно увеличить производственную эффективность и повысить уровень безопасности труда благодаря тому, что люди не будут находиться в непосредственной близости от места хранения жидкого реагента. Советом по модернизации и трансформации бизнеса АО «НАК «Казатомпром» в декабре 2020 года мероприятие КАР.03.01.М «Переход на использование водного раствора аммиака (25%) вместо каустической соды» признано завершенным в Портфеле проектов и мероприятий цифровой трансформации АО «НАК «Казатомпром».
– Известно, что компания предлагает решения и для электроэнергетики. Что из себя представляют эти проекты и какой эффект могут дать?
– В 2019 году производственным департаментом «Казатомпрома» была начата работа по изучению лучших мировых практик в сфере электроэнергетики для предотвращения аварий, связанных с перебоями по причине гололедообразования и обморожения проводов. В том же году была организована заочная встреча с российской компанией для обсуждения возможности реализации проекта на предприятии «Казатомпрома» ТОО «Уранэнерго». Совместными усилиями был проведен детальный анализ по определению проблемных участков с высокой влажностью, сильными ветрами и резкими перепадами температуры воздуха, что способствовало образованию наледи на проводах воздушных линий, а также был разработан детальный план мероприятий по реализации проекта.
В марте 2020 года данный проект одобрен Советом по модернизации и трансформации «Казатомпрома» и включен в портфель проектов цифровой трансформации. Были установлены посты контроля гололедообразования и датчики гололедной нагрузки и температуры проводов (IoT технологии). Система контроля гололедных нагрузок позволяет в режиме реального времени отслеживать на воздушных линиях электропередачи температуру воздуха, направление и скорость ветра, появление и нарастание гололедно-изморозевых отложений, прогнозировать изменения метеопараметров, а также собирать данные с датчиков, хранить их и передавать по GSM-каналу диспетчерам. Дежурный персонал отслеживает состояние линий электропередачи в режиме реального времени, что позволяет оперативно реагировать и предотвращать аварийные ситуации, своевременно уведомлять о возможных кратковременных отключениях электроэнергии добычные предприятия. Последние могут подготовить вспомогательное оборудование, минимизируя риски простоя и остановки добычи природного урана.
Реализация данного проекта в конце прошлого года позволила также улучшить условия труда персонала и снизить затраты за счет определения гололеда на высоковольтных линиях Л-111 и Л-112 без выезда на обход и осмотр бригад.
– Какие еще направления при проведении форсайт-исследования были определены как приоритетные для ГМК?
– По данным исследования, основным трендом на ближайшие 5–10 лет будет активное развитие следующих направлений: резкий рост объема промышленных данных, автоматизация и робототехника, удаленное управление производством; эффективное управление производственными активами и предиктивное техническое обслуживание и ремонт; реновация устаревшего оборудования с использованием инструментов бережливого производства и рециклинга; развитие экологии.
С учетом указанных глобальных трендов «Казатомпром» во многом шагает в ногу со временем. К примеру, по направлению «Эффективное управление производственными активами и предиктивный ТОиР» «Казатомпром» в рамках цифровой трансформации реализует соответствующий проект на основе применения международного стандарта качества ISO 55000 и серии технических методологий в области ТОиР: RCM, TPM и RBM. Также реализуется проект «Автоматизация насосного парка на основе технологии Big Data и элементов искусственного интеллекта» (Predictive maintenance). По направлению «Развитие экологии» производственным департаментом реализуется «Green Mindset – Зеленое мышление», где определены направления развития охраны окружающей среды, энергосбережения, развитие мышления работников на основе принципов «зеленой» экономики.
По направлению «Удаленное управление производственными процессами» в «Инкай» реализован проект «Умные каски», который позволяет удаленно консультировать по ремонту оборудования.
В целом в компании нацелены на создание условий для полного использования производственного потенциала предприятий атомной промышленности и готовы применять передовые практики и компетенции.
– Спасибо Вам за беседу!
Сагира Мурат