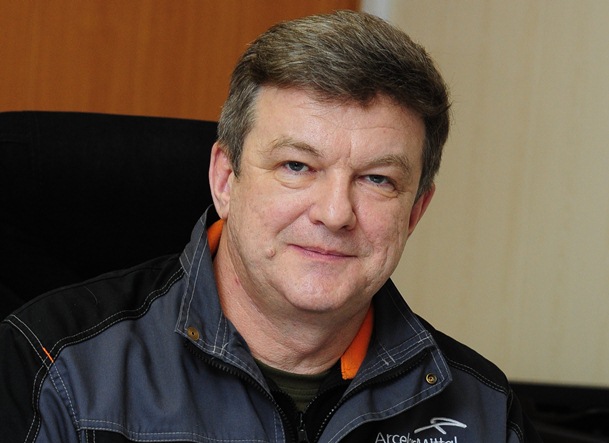
Стратегическими задачами АО «АрселорМиттал Темиртау» на ближайшие годы станут обновление материально-технической базы и диверсификация производства.
«Модернизируйся или – умрешь!» – эта фраза, прозвучавшая в одном из выступлений Президента страны Нурсултана Назарбаева, стала «крылатым» императивом для топ-менеджеров горно-металлургической отрасли республики, занятых разработкой антикризисных производственных стратегий, которые бы позволили предприятиям не просто удержаться на плаву, но и подготовить задел для нового этапа развития. Модернизация оборудования и технологий в этом стратегическом перечне занимает одну из ключевых позиций, что вполне объяснимо. По данным Министерства национальной экономики РК процент износа основных фондов ГМК в 2015 году составил 46,5%. Показатели износа оборудования и несовременность технологий вынуждают форсировать процесс их замены с учетом ресурсосбережения и высокой производительности. Причем, в отличие от юниорских компаний, чей сравнительно небольшой и «короткий» бизнес изначально базируется на современных технических достижениях, отраслевые флагманы работают десятилетиями, а потому невольно становятся заложниками прежнего технологического уклада. В составе основных фондов этих гигантов нередко находится и устаревшее оборудование, сменить которое в силу хотя бы его исполинских габаритов, мощности, а также – высокой стоимости своевременно не получается. Приходится действовать планомерно, комплексно и последовательно. А главное – без ущерба для непрерывного металлургического производства.
О том, как эта работа ведется в цехах Казахстанской Магнитки мы попросили рассказать директора по ремонтам дирекции управления АО «АрселорМиттал Темиртау» Вадима БАСИНА.
– Вадим Борисович! Перед сталелитейной промышленностью сегодня стоят две задачи: снижение энергоемкости производства и сокращение экологически вредных выбросов. Начнем с первой. В этой связи хотелось бы знать, с какими результатами на предприятии прошел энергоаудит?
– Действительно, с 2014-го по 2015 годы в крупнейшем структурном подразделении – Стальном департаменте АО «АрселорМиттал Темиртау» силами ТОО «Эл-Нур Сервис» проведен первый этап энергоаудита. Однако официальное заключение об энергоаудите согласно законодательству, выдается на юридическое лицо (включая все его подразделения). Поэтому этот документ может быть учтен оператором Государственного энергетического реестра (ГЭР) только после завершения энергоаудита Угольного департамента компании и формированию общего заключения. Соответствующий дополнительный договор с вышеупомянутой энергоаудиторской фирмой подписан. Срок окончания работ по нему с выдачей общего плана мероприятий по повышению энергоэффективности – декабрь текущего года. Но и без всяких рекомендаций в компании существует корпоративный план, предусматривающий, к примеру, снижение расходов пара и химически обессоленной, очищенной воды на тонну выпускаемой продукции. Аналогичный подход практикуется и при использовании кислорода, азота, аргона, доменного и коксового газов. Здесь упор делается на плановый ремонт трубопроводов, запорной арматуры.
Если говорить об экономии электроэнергии, то там, где технически возможно четко отследить снижение ее потребления, на комбинате давно практикуется установка частотных преобразователей. Особенно на приводы насосного и вентиляторного оборудования, что позволяет снизить расход электроэнергии до 20-30%. Эта работа ведется на предприятии уже многие годы. Частотными приводами оснащены цеха первого передела и листопрокатные, а также – конверторный цех. Кроме того, наш комбинат одним из первых в республике внедрил автоматизированную систему технического учета энергоресурсов. Сама по себе установка системы технического учета энергоресурсов – и это общеизвестный факт, – дает возможность ежедневного и постоянного контроля над потреблением энергоресурсов и способствует снижению расхода.
Эта работа будет продолжена. В планах – установка частотных преобразователей на высоковольтные приводы береговых насосных станций I-го подъема Самаркандского водохранилища. Следует подчеркнуть, что наряду с энергосбережением в компании создан специальный комитет, еженедельно занимающийся анализом себестоимости основных видов продукции – агломерата, чугуна, стали и всех видов проката.
И если комбинат работает с превышением плановых показателей по себестоимости, то проводится тщательный разбор, где и по какой причине допущено удорожание – на стадии ли рудной добычи, или в сегменте потребления электроэнергии, а, может, допущен внеплановый простой оборудования… Тотчас намечаются корректирующие меры, призванные в короткий срок привести к снижению технологических затрат.
Это очень важно для нас, наверное, еще и потому, что, имея собственную рудную базу ТОО «Оркен» в состав которого входят: Лисаковский ГОК, Атансор, Атасу и Кентюбе, а так же угольные шахты и генерирующие источники, АО «АрселорМиттал Темиртау» находится на большом удалении от своих потребителей. Поэтому в цене на его продукцию высок удельный вес транспортных расходов, особенно – железнодорожных. Отсюда это пристальное внимание к себестоимости, чтобы она была не выше, а даже ниже, чем у основных конкурентов – Магнитогорского, Новолипецкого и Череповецкого металлургических комбинатов.
– Вторая пятилетка индустриализации нацелена также на решение проблем, связанных с обновлением основных фондов как способу повысить качество выпускаемой продукции и производительность труда. Какие меры предпринимаются АМТ в этом направлении?
– Хотелось бы напомнить, что ежегодно компания «АрселорМиттал Темиртау», имея стратегическую программу модернизации основных фондов, за счет собственных средств и кредитных займов, осуществляет большую работу по замене устаревшего оборудования, проведению капитальных ремонтов и реконструкции металлургических переделов.
В рамках этой программы за последние годы проведена модернизация доменных печей №2 и №3 с увеличением их объема и изменением конструкции литейного двора (укрытые желоба), установкой бесконусных загрузочных устройств. Обе домны оснащены оборудованием на принципиально более высоком уровне автоматизации металлургических процессов и системы очистки отходящих газов.
Применение новых типов огнеупорных материалов позволило увеличить объем печей. На домне №2 – с 1717 до 2240 метров кубических и на домне №3 – 3200 до 3840 кубических метров. В настоящее время завершена модернизация доменной печи №4, в результате чего объем печи увеличился с 3200 до 3440 кубических метров. В первой декаде ноября выполнены необходимы предпусковые работы (сушка кладки, настройка систем автоматики и контроля процесса, загрузка печи) 8 ноября печь была задута и 11 ноября металлурги получили на этом обновленном агрегате первый чугун.
Таким образом, к концу года компания подошла с тремя современными работающими домнами. До стабилизации технологических параметров ДП-4 и выхода на запланированные объемы, доменная печь №1 будет находиться в эксплуатации, а затем остановлена. Три действующие печи позволят комбинату производить до 14 тыс. тонн чугуна в сутки.
Следующий этап – модернизация агломерационных машин № 5, 6. В 2015 году выполнена реконструкция агломашины №7. В следующем – намечено модернизировать АМ №6, а еще через год АМ №5. То есть, каждый год – по агломашине, с последующей установкой электрофильтров за зоной спекания. В кислородно-конвертерном цехе будет установлена третья печь-ковш, улучшив тем самым технологический процесс и покончив с фактами совпадения циклограмм при работе разливочных машин.
Продолжается модернизация прокатных станов. Каждый год в ходе капитальных ремонтов нами проводится и обновление их оборудования. Так, например, с 21 октября по 5 ноября в ремонте находился стан горячего проката ЛПЦ-1. В итоге выполнен большой объем работ: завершена модернизация летучих ножниц с новой системой управления, осуществлена замена станины на моталке № 2 и введена новая схема управления. В ближайшем будущем планируем перейти с вертикальной на горизонтальную ось транспортировки рулонов от обвязочных машин. Это позволит избежать травмирования рулонов при транспортировке и снизить потери металла.
Не скрою, по некоторым цехам у нас наблюдается серьезный износ оборудования. Во-первых – на аглофабрике, которая эксплуатируется уже около полувека, во-вторых – на коксохимическом производстве, состоящем из шести коксовых батарей. Как показывает анализ работы КХП, основные простои оборудования приходятся на следующие агрегаты: коксовыталкиватели, загруз-вагоны, тушильные вагоны и двересъемные машины. Но нами принимаются меры по их ремонту, а главное – постепенной замене оборудования.
Третий год ведется эта работа. И хотелось бы подчеркнуть, что с проблемой высокого износа основных фондов сталкиваются многие металлургические предприятия СНГ. На сегодняшний день в металлургию направляются инвестиции только после углубленного анализа их необходимости. Слишком неопределенная ситуация складывается на рынке в связи с падением цен на металлы и высокой конкуренцией. Поэтому инвестировать в модернизацию, надеясь только на будущее, уже никто не рискует. Все вкладывают деньги целенаправленно и только по мере необходимости.
– Каковы планы крупнейшего подразделения АО «АрселорМиттал Темиртау» – Стального департамента по такому антикризисному направлению, как диверсификация производства?
– Диверсификация деятельности предприятия в условиях рыночной нестабильности позволяет минимизировать риски. Поэтому компания в ближайшие годы сохранит курс на диверсификацию производственных мощностей и технологической базы, начав, как уже говорилось выше, с модернизации. Это ускорит решение задачи по выпуску новых, экономически выгодных для АМТ видов металлургической продукции, улучшит качественные параметры товарной номенклатуры, производимой в настоящее время, а также – окажет стимулирующее влияние на рост объёмов добычи сырья, сократит дефицит энергоресурсов.
В частности, реконструкция шестиклетевого стана холодной прокатки 1400, в ходе которой увеличилась ширина прокатываемой полосы и модернизирована система автоматического контроля поперечного профиля прокатываемой полосы, позволили обеспечить стабильную загрузку линий оцинкования качественным и востребованным рынком «тонким» (0,25-0,40мм) и «широким» (до 1265 мм) стальным прокатом. Также расширен номенклатурный сортамент холоднокатаной продукции отвечающей требованиям зарубежных стандартов.
С модернизацией черновой и чистовой группы клетей непрерывного стана горячей прокатки 1700, его производительность возросла в полтора-два раза, вдобавок – появилась возможность катать горячекатаную полосу с улучшенными характеристиками геометрических размеров, поперечного профиля, отвечающую современным требованиям рынка.
Уже сегодня просматривается перспективная и новая для АО «АрселорМиттал Темиртау» тенденция – производство и сбыт продукции первого передела: непрерывно литых заготовок, слябов и литого чушкового чугуна, а также вторичных продуктов, образующихся в процессе производства, для химической и строительной индустрии.
Поэтапная концепция продуктовой диверсификации нацелена на освоение новых экономически выгодных, не ключевых рынков металлопродукции, удовлетворяющей растущие потребности потребителей. К примеру, в горячекатаном прокате бейнитных марок сталей для магистральных нефтегазопроводов. Или — в прокате повышенной прочности для судостроения и изготовления сосудов высокого давления, а проведенные капитальные ремонты позволят темиртауским металлургам достичь увеличения производственных мощностей до 4,5 млн. тонн металла в год.
– Как и все крупные предприятия чёрной металлургии, АО «АрселорМиттал Темиртау» оказывает серьезное влияние на экологическую обстановку в Темиртау. Отсюда вопрос: в чем заключается природоохранная деятельность компании?
– Охрана окружающей среды для «АрселорМиттал Темиртау» – больше чем обязанность. Это – важнейшая составляющая долговременной политики социальной ответственности.
Напомню, в 2015 году компанией завершен один из самых значимых для города экологический проект по реконструкции газоотводящих трактов конвертеров № 1-3 с вводом в эксплуатацию систем первичной газоочистки и вторичной – для улавливания неорганизованных выбросов оксида железа. Установленное оборудование – скруббера и рукавные фильтры позволили снизить концентрацию пыли в отходящих газах с 680 до 45 миллиграммов на кубометр. Экологические проекты реализованы также в доменном, агломерационном, коксохимическом производствах.
За последнее пятилетие выбросы загрязняющих веществ в атмосферу сокращены более чем на 60 тысяч тонн, в том числе по пыли – на 9,3 тысячи тонн. Удельные выбросы на тонну стали в целом снизились с 79,1 до 65,7 килограмма. Кроме того, понимая, что металлургия всегда связана с высокими температурами и процессами окисления, на комбинате претворяются в жизнь проекты, направленные на сокращение выбросов парниковых газов. Так, в свое время в рамках ПФИИР был введен в эксплуатацию комплекс водоподготовки и котельной, работающей на доменном газе.
Год назад в Темиртау на границе санитарно-защитной зоны предприятия установлены три системы контроля качества воздуха – от компании OPSIS, позволяющие в режиме постоянного автоматического мониторинга отслеживать параметры окружающей среды и оперативно реагировать на их изменения.
В следующем году АО «АрселорМиттал Темиртау» намерено приступить к достаточно большому по своим объемам и затратам проекту – реконструкции системы очистки коксового газа и очистных сооружений коксохимического производства.
Фактически речь идет о строительстве нового цеха по улавливанию химических продуктов, монтаже и запуске мощной биохимустановки, что, несомненно, скажется на улучшении качества промстоков, сбрасываемых комбинатом на очистные сооружения, и состоянии атмосферного воздуха на границе санитарно-защитной зоны комбината.
«Горно-металлургическая промышленность» №10-11 2016 Светлана Егорова